Spider Fitting Toughened Glass Manufacturer in Peenya
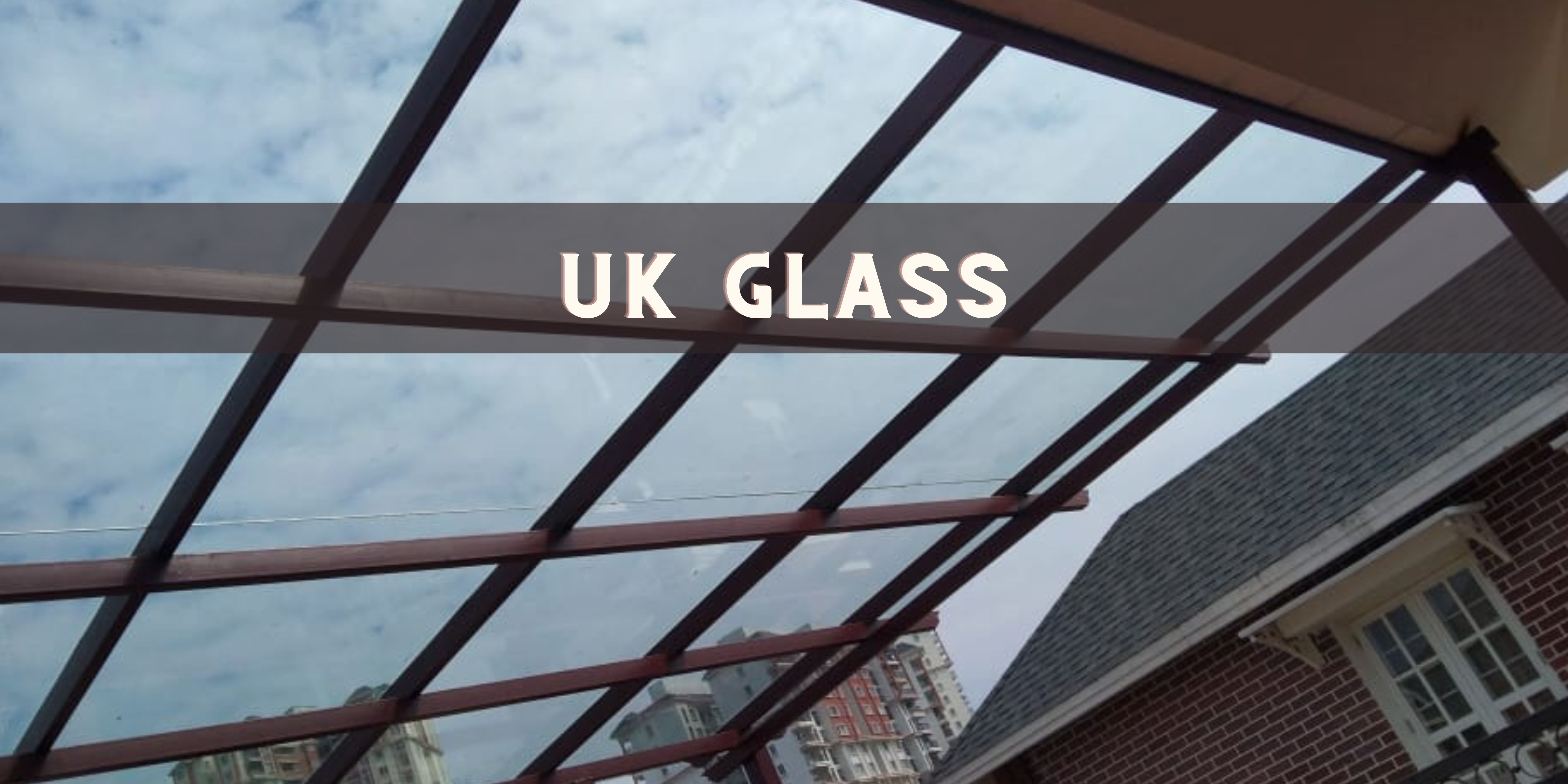
Contact : +919743712272
Spider Fitting Toughened Glass Manufacture
Introduction
Spider fittings are crucial components in modern architecture, used to create striking glass facades and structural glass systems. They provide both functional support and aesthetic appeal by allowing large expanses of glass to be fixed without the need for extensive framing. The manufacture of spider fittings and toughened glass involves precise engineering and high-quality materials to ensure durability, safety, and aesthetic excellence.
Toughened Glass Manufacturing
Toughened glass, also known as tempered glass, is a type of safety glass that is treated to be much stronger than ordinary glass. It is produced through a process of extreme heating and rapid cooling, which makes it highly resistant to impact and thermal stress.
-
Raw Material Preparation: The process begins with the selection and preparation of raw materials. The primary component is silica sand, which is mixed with soda ash, limestone, and other additives to form the glass batch. These materials are carefully measured and mixed to ensure the desired quality of the glass.
-
Melting: The glass batch is fed into a furnace and heated to a temperature of around 1,600°C (2,912°F). This high temperature melts the batch into a molten glass.
-
Forming: The molten glass is then shaped into the desired form. For toughened glass, it is usually formed into sheets of various sizes and thicknesses. The forming process involves floating the molten glass on a bed of molten tin to create a smooth, flat surface.
-
Annealing: The glass sheets are gradually cooled in a controlled environment in a process called annealing. This step is crucial for relieving internal stresses and ensuring uniform thickness.
-
Cutting and Edgework: Once cooled, the glass is cut into specific sizes and shapes based on requirements. Edges are polished and finished to avoid sharp edges that could pose safety risks.
-
Toughening: The cut glass sheets are then subjected to the toughening process. This involves heating the glass to about 620-650°C (1,148-1,202°F) and then rapidly cooling it. The process creates compressive stresses on the surface of the glass and tensile stresses inside, which significantly increases its strength and resistance to impact.
-
Quality Control: Rigorous quality checks are performed to ensure that the toughened glass meets safety and performance standards. This includes tests for thermal stress resistance, impact resistance, and optical clarity.
Spider Fitting Manufacturing
Spider fittings are used to attach glass panels to structural elements and are named for their resemblance to a spider’s legs. They are typically made from stainless steel due to its durability and resistance to corrosion.
-
Design and Engineering: The design of spider fittings involves precise engineering to ensure they can support the glass panels effectively. This includes calculations for load-bearing capacity, stress distribution, and aesthetic considerations.
-
Material Selection: Stainless steel is the preferred material for spider fittings due to its strength, resistance to environmental factors, and aesthetic qualities. The stainless steel used is typically of high quality, such as grade 304 or 316, which offers excellent corrosion resistance.
-
Fabrication: The manufacturing process begins with cutting the stainless steel into the required shapes. This is followed by machining processes such as turning, drilling, and milling to achieve the precise dimensions and features required for the fittings.
-
Assembly: After fabrication, the individual components of the spider fittings are assembled. This includes attaching the spider arms, fixing bolts, and other hardware. The assembly process is performed with high precision to ensure that the fittings will function correctly when installed.
-
Finishing: The assembled spider fittings undergo a finishing process to enhance their appearance and durability. This may include polishing, passivation (to enhance corrosion resistance), and electroplating (for additional protection and aesthetic appeal).
-
Testing and Quality Control: Each spider fitting is subjected to rigorous testing to ensure it meets structural and safety standards. This includes tests for load-bearing capacity, durability, and dimensional accuracy.
Installation and Application
Once the spider fittings and toughened glass are manufactured, they are ready for installation. The process typically involves the following steps:
-
Site Preparation: The installation site is prepared by ensuring that the structural elements are correctly aligned and ready to receive the glass panels and fittings.
-
Glass Handling: The toughened glass panels are carefully transported to the site and handled using specialized equipment to avoid damage.
-
Fitting Installation: The spider fittings are installed on the structural elements, and the glass panels are mounted onto the fittings. Precision is crucial during installation to ensure that the glass panels are properly aligned and secured.
-
Sealing and Finishing: After the glass panels are installed, any gaps between the glass and the structural elements are sealed with silicone or other appropriate sealants to prevent water ingress and enhance thermal insulation.
-
Inspection: A final inspection is conducted to ensure that everything is installed correctly and that the installation meets all safety and performance standards.
Conclusion
The manufacture of spider fittings and toughened glass is a sophisticated process that combines advanced technology with skilled craftsmanship. Toughened glass provides durability and safety, while spider fittings offer a sleek and modern way to support and display glass panels. Together, they enable the creation of stunning architectural features that are both functional and visually striking.