Glare Glass Manufacturer Bangalore
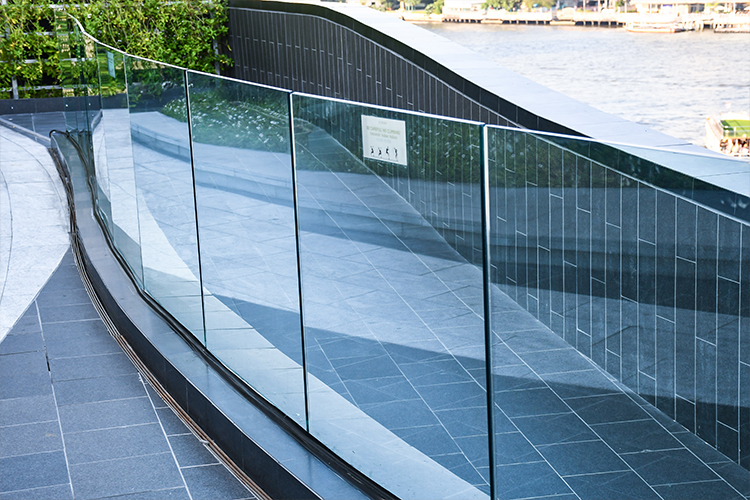
Contact : +919743712272
Glare Glass Manufacturing
Glare glass, commonly known as anti-glare or anti-reflective glass, is a specialized type of glass designed to minimize reflections and enhance visibility. This innovative product is increasingly utilized in various applications, including architectural glass, automotive windows, eyewear, and electronic displays. The manufacturing process of glare glass involves several advanced technologies and techniques, resulting in a product that improves comfort and safety by reducing glare and reflections.
Understanding Glare and Its Impact
Glare occurs when bright light reflects off surfaces, causing discomfort and reducing visibility. In environments such as offices, homes, and vehicles, excessive glare can lead to eye strain, fatigue, and decreased productivity. To combat this, glare glass is engineered to diffuse light and minimize reflections, providing a clearer and more comfortable viewing experience.
Manufacturing Process
The manufacturing of glare glass typically involves the following steps:
-
Raw Material Selection: The process begins with the selection of high-quality raw materials, primarily silica sand, soda ash, and limestone. The purity and composition of these materials significantly affect the optical properties of the final product.
-
Melting: The raw materials are mixed and melted in a furnace at temperatures exceeding 1,500°C (2,732°F). This molten glass is then poured into molds or formed into sheets using various techniques such as float glass production, where molten glass is floated on molten tin to create flat sheets.
-
Annealing: After forming, the glass sheets are gradually cooled in an annealing lehr. This controlled cooling process relieves internal stresses and ensures uniform thickness, which is crucial for the optical performance of the glass.
-
Surface Treatment: The most critical step in glare glass manufacturing is the application of anti-reflective coatings. These coatings are typically made of multiple layers of thin films that utilize interference effects to reduce light reflections. The coating process may involve techniques such as sputtering or chemical vapor deposition (CVD).
-
Quality Control: Throughout the manufacturing process, rigorous quality control measures are implemented. This includes testing for optical clarity, thickness, and resistance to scratching and environmental factors. Advanced testing methods like spectrophotometry are used to measure the effectiveness of the anti-reflective properties.
-
Cutting and Finishing: Once the glare glass has passed quality checks, it is cut to size according to customer specifications. Edges may be polished, and additional finishing processes such as tempering or lamination may be applied to enhance durability and safety.
Applications of Glare Glass
Glare glass has a wide range of applications across various industries:
- Architecture: Used in windows and facades, glare glass improves natural light entry while minimizing heat gain and glare, enhancing energy efficiency in buildings.
- Automotive: Anti-glare glass is utilized in windshields and side windows, improving driver visibility and safety by reducing reflections from headlights and sunlight.
- Eyewear: Prescription and sunglasses often feature glare-reducing coatings, enhancing visual comfort and clarity for users.
- Electronics: Displays on devices such as smartphones, tablets, and televisions employ glare glass to improve visibility under bright conditions.
Conclusion
The manufacturing of glare glass combines advanced materials science with innovative engineering techniques to produce a vital product that enhances visibility and comfort across various applications. As technology continues to evolve, the demand for glare glass is expected to grow, leading to further advancements in manufacturing processes and applications, ultimately improving the quality of life for consumers in many sectors.